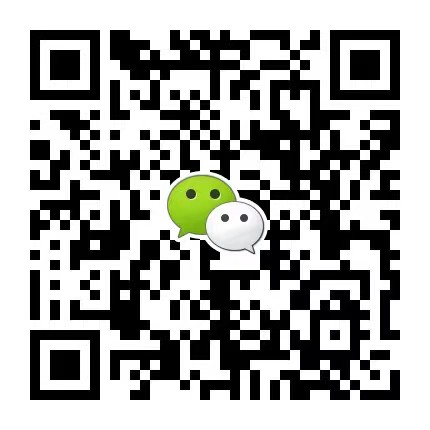
發布日期:2022/6/24 9:42:10 訪問次數:1380
一.擦傷:
特征:鋼管表面呈現長短不一,方向不定的無規則的擦痕,一般呈直線形,均能看到其底。
產生原因:1)退火時操作不當;
2)在吊運中劃傷;
3)在矯直過程中,鋼管在套筒處擦傷。
二.劃道(又稱拉絲、拉毛、直道包括青線)
特征:鋼管內外表面上呈現縱向直線形的長短不一劃道,外為溝狀,可見底,表面有損傷內劃道,表面無損傷直線。
產生原因:1)毛管上劃道;
2)毛管上殘存有氧化鐵皮; 3)潤滑劑涂層不良,引起摩擦力增加,致使模具發熱焊接金屬;
4)內外模具硬度不夠或不均,光潔度差;
5)錘頭不良,過渡部分產生尖銳的棱角,模具磨損,造成劃道。
三.抖紋:
特征:在鋼管內外表面上,沿長度方向呈高低不平的整圈或半圈波形的環痕,逐個相間排列,有連續的,也有斷續的。一般由拉拔動時抖動(稱“打機槍”)所造成。
產生原因:1)酸洗過程未沖凈,潤滑不良,涂層不均;
2)退火性能不均勻,抗拉強度過大,含碳量較高的熱軋鋼管冷卻速度過大,造成鋼質較硬,加工硬化;
3)管子過大,頭部無空隙,皂化不良;
4)芯棒細,拔制時芯棒產生彈性變形,引起抖動;
5)拉拔時啟動速度過快,或開拉時鏈條振動;
6)配模不合理,入口錐角太大,管與??捉佑|面積小,或模具定徑位置不當,拔制時變形不穩,定面抖動。
四.凹坑(包括壓痕):
特征:鋼管表面呈面積不一的局部凹陷,有的呈周期性,也有的無規律。缺陷表面有破傷為凹坑,表面無破傷的為壓痕。 產生原因:1)由于氧化鐵皮或其他質硬的污物粘附在鋼管表面,在拔制或矯直中壓入鋼管表面后剝落而留下壓痕;
2)矯直輥粘附了異物,在矯直過程中鋼管表面壓成凹坑;
3)原先存在于鋼管表面的翹皮剝落。
五.麻點:
特征:鋼管表面成片的點狀細小凹坑。
產生原因:1)酸洗時產生點狀腐蝕;
2)退火后氧化鐵皮過厚矯直后壓入了鋼管表面;
3)鋼管保存不好產生銹蝕;
4)氧化皮未清洗干凈,拉拔壓入管面,產生麻點; 5)管面有油污,退火時局部燒成麻面。
六.翹皮:
特征:鋼管內外表面局部與金屬基體分離的薄層,呈塊狀或鱗狀,不連續,有管壁上生根或不生根,但不能自然剝落。
產生原因:1)鋼質不良,有皮下氣泡,經冷拔后暴露;
2)由熱軋產生帶至冷拔或冷拔管上;
3)鋼管原有較深并有棱角的橫向凹坑,經拉拔后形成;
4)鋼管尾中彎曲造成內側減徑量過大,在拔制時受力不均,形成內翹皮。
七.離層:
特征:在鋼管管壁中呈螺旋方向的分層破裂。
產生原因:1)管坯中有非金屬夾雜物及縮孔殘余;
2)嚴重的疏松等。
八.裂縫:
特征:鋼管內外表面上,呈塊直線或螺旋分布的細小裂紋,其兩端和底部是尖形的,有連續的和不連續的。
產生原因:1)鋼質不良,有皮下氣孔和皮下夾雜物;
2)拔制前鋼管上有裂紋或較深的麻點;
3)退火不當。
下一信息:無縫鋼管壓力